Our Capabilities >
- Design
- Tooling
- Molding
- Assembly
- Fulfillment
- Quality
Quality
Fully qualifying our molds prior to shipment and start-up in the production facility is a critical step in Univac's start-to-finish service mold process. Our molds are fully qualified in our dedicated mold testing center, and plastic parts are validated in our metrology laboratory. Our process and QC engineers have in depth knowledge of mold validation and various industry validations protocols (IOP/Q ; PPAP) documentations.
Detailed mold qualification requirements are typically established based on the customer's input. Key objectives include proving mold functionality, producing quality plastic parts, and developing an acceptable process window at the fastest cycle time. For export toolings, we provide our customer a complete qualification report with the mold manual outlining process and installation parameters.
Plastic part metrology typically includes first article inspection (FAI), visual inspection, and final acceptance test (FAT) measurements.
Univac has a dedicated in-house metrology laboratory. The lab's multi-shift operation supports Univac's mold testing center mold qualifications, production facility and customers' metrology inspection needs. The lab has a full suite of measurement equipment including: CMM (ZEISS), Smart Scope (OGP), Smart Scope (Micro VU), TMS (NIKON), Gear Tester (MAHR), Moisture Analayser (METROHM) & digital calipers and gauges.
Quality Systems
cGMP, ISO 9001, ISO 13485, ISO 14001, TS 16949
Clean Rooms (Class 100,000 and Class 10,000)
Clean room assembly
Service and Capabilities Include
- First article inspection (FAI)
- Cpk study
- Visual Inspections
- Gage R&R
- Steel measurements
- Design of experiments (DOE) inspection
- Physical testing (drop, lift force, leak test, etc)
- Custom fixture designs
- In process inspection
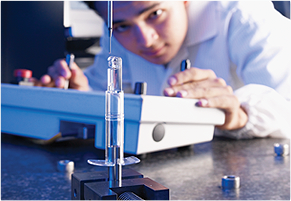